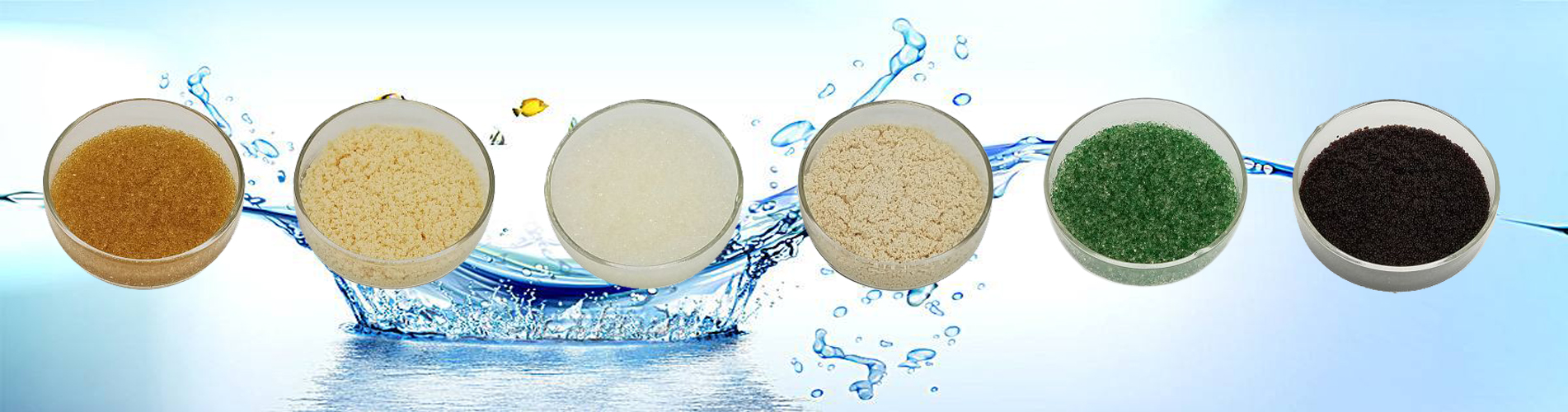
Iron poisoning treatment of ion exchange resin
Ion exchange resin has the advantages of good chemical stability, high mechanical strength, and large exchange capacity, so it has been widely used in the water treatment of power station boilers and industrial boilers, as well as in the production of demineralized water and purified water. However, during the use of the resin, due to the pollution of harmful impurities (such as ferrites, organics, etc.), resin "poisoning" accidents will occur. If reasonable measures are not taken to revive the resin in time, the resin may become invalid or even scrapped. Iron poisoning is common in resin poisoning. Next, based on years of production practice, the author will talk about the treatment and preventive measures for this kind of resin iron "poisoning" accident.
There are also two main reasons for iron poisoning of anion resin: first, the alkali purity of regenerated anion resin can not reach the specified standard, especially when there are many compounds containing iron in liquid alkali, it is easier to poison anion resin; Second, when macromolecular organic substances are contained in the water, it is easy to form chelates (i.e. organic iron) with iron, which can exchange with strong alkaline anion resin, concentrate on the position of exchange group, block the exchange channel of resin, reduce the exchange capacity and regeneration capacity, reduce the re effectiveness rate, increase the consumption of regenerant and cleaning water, and further lead to "poisoning" of resin iron.
2 Pollution identification method
2.1 Appearance color identification
From the appearance, the color of the resin with iron poisoning changes from transparent yellow (cation resin) or milky white (anion resin) to dark, even black in severe cases.
2.2 Test identification
It is a more accurate method to determine the degree of resin iron poisoning by measuring the iron content in water.
The method is as follows: wash the "poisoned" resin with clean water, soak it in 10% salt water for regeneration for about 30min, pour out the salt water and wash it with distilled water (or demineralized water) for 2-3 times, take out part of the resin and put it into a test tube or glass bottle, then add 6mol/L hydrochloric acid (about twice the volume of the resin), cover it tightly and shake it for 15min, then take out the acid solution and inject it into another clean test tube, and drop it into the saturated potassium ferrocyanide solution, The degree of "poisoning" of resin iron can be judged from the color of Prussian blue generated from the test solution (from light blue to brown black).
It should be noted that some units only use the method of measuring resin exchange capacity to judge whether the resin is iron "poisoned", which is inaccurate. Because iron "poisoning" only reduces the working exchange capacity of the resin, but has little effect on the full exchange capacity.
3 Recovery treatment method
Since the exchange capacity of iron poisoned resin can be restored after proper treatment, the resin should be properly treated after iron poisoning, otherwise the possibility of resin damage will increase and the resin will be scrapped.
There are mainly three recovery methods for iron "poisoned" resin, which are compared as follows:
3.1 Mechanism of hydrochloric acid resuscitation method: the selection order of strong acid resin for cations is: Fe3+>Fe2+>Ca2+>Mg2+>Na+>H+. After adding 10% hydrochloric acid to the iron "poisoned" resin, hydrochloric acid will remove colloidal Fe2O3 from the resin surface or gel pore? XH2O dissolves into Fe3+, and at the same time, H+in hydrochloric acid exchanges with Fe3+, Ca2+, Mg2+on the resin, so that the resin gradually turns into hydrogen type, and then into sodium type before operation. This method is simple and practical. However, in practical application, in order to fully "poison" the resin with cycads, the concentration of hydrochloric acid must be increased to more than 10%, which not only increases the treatment cost, but also easily damages the anti-corrosion coating of the exchanger.
3.2 Hydrochloric acid salt resultation method
Mechanism: 4% hydrochloric acid and 4% salt solution are added into the "iron poisoning" resin and fully soaked. The main function of hydrochloric acid is to dissolve Fe2O3? XH2O。 Na+in table salt and H+in hydrochloric acid are exchanged with Fe3+, Fe2+, Ca2+, Mg2+on the resin, so that the resin is gradually transformed into sodium hydrogen mixed type, and it can be regenerated into sodium type before operation.
This method is a common one. However, there are also some shortcomings, such as large amount of hydrochloric acid and table salt, long time consumption, and incomplete recovery treatment.
3.3 Hydrochloric acid salt sodium sulfite resuscitation method
Mechanism: The mixed solution of 4% hydrochloric acid, 4% salt and 0.08% sodium sulfite is added into the iron "poisoning" resin for full immersion. The effect of hydrochloric acid and salt is the same as above. The S in Na2SO3 reduces SO32-Fe3+to Fe2+, thus reducing the resin's binding to Fe3+, and the H+generated by the reaction can promote Fe2O3? Dissolution of XH2O, reaction formula:
SO32-+2Fe3++H2O≒SO42-+Fe2++2H+
Finally, sodium hydrogen mixed resin can be converted into sodium resin and put into use.
It should be noted that the concentration of Na2SO3 should be determined by experiment and should not be greater than 0.1% generally, because the concentration of Na2SO3 is too high, which is easy to produce SO2 gas, and the increase of the concentration of SO42 - will produce CaSO4 precipitation.
The practice has proved that this method is an ideal method for treating iron "poisoned" resin with less consumption of resuscitator, short time, low concentration of hydrochloric acid in resuscitator, less corrosivity to exchanger and better resuscitative effect.
Categories
latest blog
© Copyright: 2025 Bengbu Sanyi Resin Technology Co., Ltd. All Rights Reserved.
IPv6 network supported